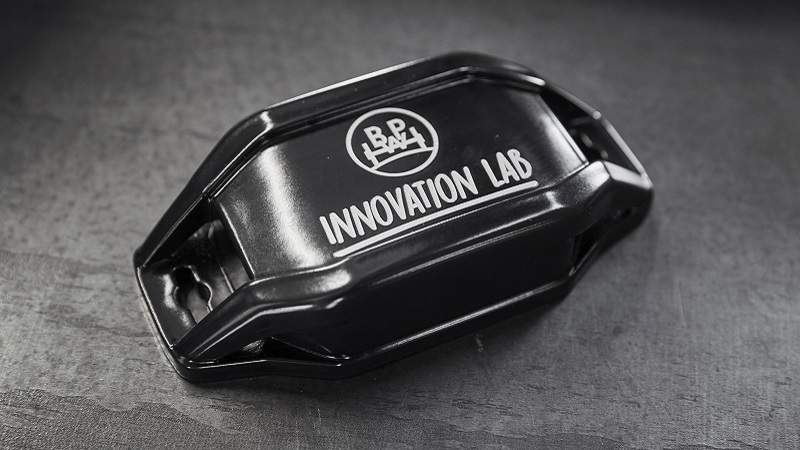
Where’s my shipment? No more logistics black holes
In the past, freight consignors would find out that their goods were not going to arrive on time once it was literally too late. Neither the purchaser, nor the seller, nor the consignor knew where the goods were and if there was still a chance they might arrive on time. But a team consisting of radio technology and cloud services now helps to provide this much needed information. Shipments can be monitored from start to finish. And as a result, logistics processes run more smoothly and new business models in the logistics industry emerge. So just exactly how does this duo of radio and cloud work?
Too much transparency is not a luxury freight consignors have these days. Once a shipment leaves the loading dock, the exact location of the goods is unknown until they reach their destination. And this happens later than planned and expected very often.
The Internet of (rolling) Things wants to put an end to this. One way to shine a light into the black abyss of information – from the time a shipment is loaded to the time it is unloaded – is to use a freight tracker. A freight tracker is an industrial device that is attached to a load carrier and provides current location information on a regular basis. What does this have to do with the Internet of Things? This type of tracker, for example, BPW Innovation Lab’s CargoTracer, sends the data it records, such as geo-coordinates and ambient temperature, to a cloud service. In the case of CargoTracer, data is sent to various Azure solutions, such as Azure Location Based Services, which also contribute traffic information, among other things. What are the user’s benefits? The software automatically calculates the probable arrival time.
These types of trackers are possible thanks to ultra narrow-band radio technology – developed specifically for the Internet of Things – from the French provider, Sigfox. The wide-range technology consumes little energy, since 12-byte data packets are transmitted only every 20 minutes. The CargoTracer’s battery is designed to last up to two years.
Azure is ideal for projects in their infancy. Companies don’t need to build or run their own, extensive infrastructure and can use turnkey components such as Location Based Services. This is an immense advantage in a competitive market where pace is an important factor for success. Furthermore, it takes only a push of a button to expand the cloud infrastructure as requirements and the number of users grow. To access dashboards, users log on to their management portal using Azure Active Directory B2C. The portal displays the current location of their shipment and also the expected delivery time.
BPW benefits from yet another advantage of having a cloud architecture – open interfaces. They are used to transfer data to the consignor’s ERP system. Customer service employees see all of the shipments’ relevant order data in a familiar software environment and at a glance.
By the way, the cloud also makes it possible to determine the contents of containers with operating materials. How?
Find out by reading the full description of the BPW Innovation Lab CargoTracer project.