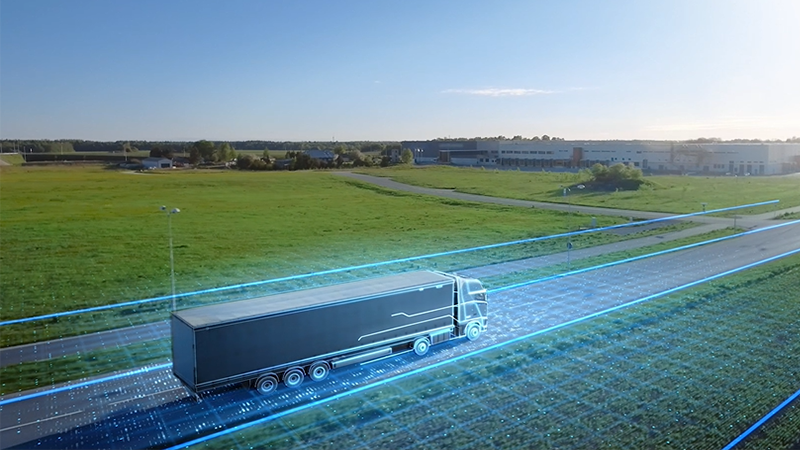
Making The Invisible …. Visible!
Manufacturing processes in the automotive industry is evolving at a fast pace towards being more adaptable, resilient & sustainable. As the technology path is clearly anchoring towards use of Electric Vehicles and Fuel Cell Vehicles, the manufacturing ecosystem needs to evolve in parallel on similar lines. An electric vehicle is like a living organism, eAxle, steering systems, brake systems, powerpacks etc. form the formidable aspect of electromobility, there is one unsung yet supercritical component which must work relentlessly to keep the vehicle mobile & this critical component is called ELOP (Electric Oil Pump).
Just like a human heart which pumps blood to the organs of the body, Electric Oil Pump circulates fluid to keep all the critical components of the vehicle functional. Therefore, they are needed to keep the electric axle lubricated and ensures that electric motor and rotors are not over heated. Failure is not an option for this component! Because when it stumbles, the whole vehicle stumbles and this can severely impact people transportation, supply chain, logistics & manufacturing activities.
With a vision to enable sustainable transportation and stationary applications, secure & reliable, VHIT has now evolved a manufacturing ecosystem which will make the pumps that they manufacture intelligent, and which can communicate. Be it on the manufacturing line when it is being produced or when it is operational on a vehicle, the pump can alert when it needs help and people can inspect the pump digitally no matter where the pump is, as long as the pump is connected to Azure. This digital feature seamlessly integrates into the connected vehicle ecosystem & the OEMs could inspect them remotely. In the near future the pump will be able to communicate its health condition directly to driver’s smartwatch or to smartphone, while algorithms running on OEM or VHIT’s ecosystem can help in predicting possible future issues and alert the driver.
Are you wondering how did this happen?
VHIT in close collaboration with Bosch & Microsoft have developed the Digital Twins which serves as brain for these pumps. The pumps are now connectivity enabled & can interact with Azure ecosystem. Digital Twin lets these pump talk in real time every time.
Digital Twin for VHIT brings two-fold benefits,
1. The manufacturing ecosystem of VHIT becomes smart. While manufacturing & before dispatch, customers of VHIT can now experience testing of pumps & enhance reliability topics via cloud
2. When assembled on a vehicle, the pump will communicate with the vehicle OEM & the driver of the vehicle as well.
Upon scaling, this solution will provide situational awareness to know the health of thousands of Electric Oil pumps on the vehicle at present and millions of them in future. This actual field feedback will enable VHIT to innovate & further value add to functional & reliability aspects of pump. This data driven advantage can be harvested to improve the efficiency levels of electromobility.
On the other hand, the vehicle OEMs will now have access to real time condition of each pump on the field and any possible issue can be identified before it’s too late. Moreover, each of these pumps can be identified very fast, replaced and analyzed thus reducing the time for root cause analysis and enhancing end customer satisfaction.
When Alessandro Fauda, who heads the Engineering Department in VHIT talks about innovation, the excitement in his voice is audible. The point is to reduce complexity and make people’s jobs easier.
Automotive Industry is going through a fast transition and moving towards being more sustainable. One of the major innovation areas is the area of digitalization and connectivity. Alessandro is always connected to European Community of Innovation through EIT and Horizon Projects. He says that a lot of focus for the innovation has always been on bigger components of the Electric Vehicle like Electric Axles, Batteries etc. & the unacknowledged were the auxiliary components.
The auxiliary component that Alessandro talks about is the Electric Oil Pump (ELOP) that is the heart of an Electrical vehicle. It is solely responsible for providing lubrication of e-axle gears and cooling of high-power density e-motor stator and rotors. The importance of this component keeping on running is vital. If it stops, then the vehicle stops. The impact is pronounced heavily on commercial vehicles, every stop time in here is a direct revenue loss to the customer. VHIT has addressed this problem by collaborating with Bosch & Microsoft introducing the Digital Twin of the electric oil pump that runs on Azure.
Interesting also is how the idea of developing Digital Twin came into being. The motivation and need were foreseen through the Horizon project about what vision EU sees for the European OEMs to preserve the competitiveness and sustainability of the electric and fuel cell vehicles. VHIT has taken this clue and developed Digital Twin, which can seamlessly integrate with customer Digital Twin of electric and fuel cell vehicles. The design of the Digital Twin for ELOP was from grounds up, was done keeping in mind modularity and easy integration with customer’s own system’s Digital Twins.
The Digital Twin of ELOP that VHIT also calls virtual ELOP (VELOP) makes it possible to know the health of each pump on the Vehicle when they are running in real time. The system takes in real time measurement from the ELOP and gives information on the health of different critical components of pumps for example capacitors, sealing, windings and rotor magnets. Through the digital twin of ELOP, VHIT is bringing the power of cloud and innovation to the fundamental levels of Automotive Components. The solutions not only helps VHIT’s customer bring value but also allows Electric Vehicle and Fuel Cell Vehicle customers to be aware of the health of not just E-axle, Battery but also the components which are vital to keep these working.
Already the topics in Horizon projects demand for Digital Twin of these components. Unfortunately, at the auxiliary component level, this innovation is not pushed, and this is where we see VHIT taking a lead and moving ahead of the curves. VHIT therefore is not just providing the physical product but also the virtual one
Alessandro Fauda, Head of Engineering, VHIT
We firmly believe that Digital Twins will open huge opportunities for improvement in the area of automotive component manufacturing and will drive enhancement for the vehicle OEMs who integrate them on their vehicles
Jalal Khan, Engineering & Innovation Expert, VHIT
The Digital Twin enables the implementation of virtual sensors as well to measure the temperature of every critical electronic and electrical components which is otherwise not possible by real physical sensors due to very compact dimensions of ELOP
Manish Kumar, Mechatronics & Simulation Expert, VHIT
As the electromobility market evolves rapidly, it becomes fundamental to continuously innovate and bring value to our customers. We have transformed from Mechanical to Mechatronics and now with Digital Twins we are redefining the product innovation at VHIT. With this we are building the bricks needed to complete the Automotive digital ecosystem
Emanuele, Head of Prototyping and Testing, VHIT
By leveraging Microsoft technologies and engineering expertise of Bosch we have enabled VHIT3 to create market differentiators for their customers
Bhuvan Shetty, Global Strategic Partnership & Sales, Bosch
Bosch has enabled VHIT to build the connected pumps, a digital highway which brings complete transparency in the value chain of the pump manufacturing and a communication channel between intra companies to collaborate seamlessly
Prahallad CR, Partner: Customer Solutions, Bosch
This is a great example to show case how Azure enables companies to drive combinatorial innovation to connect people, products and processes. A great example of how Digital Twins in industrial environment can make a real difference
Till Hertwig, Industry Executive Manufacturing, Microsoft