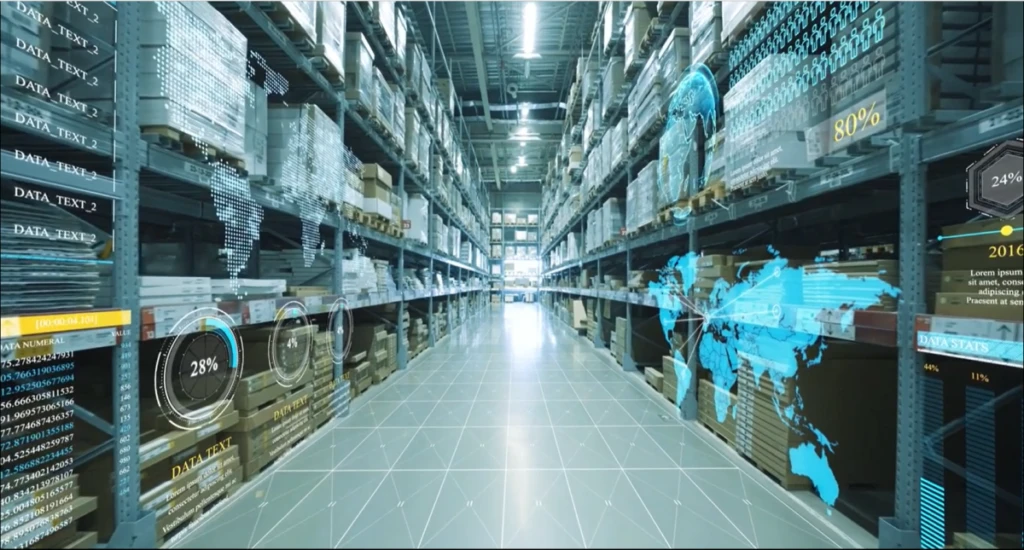
Microsoft fuels digital transformation of supply chains for a resilient and sustainable future
We are excited to share two new investments in Microsoft Dynamics 365 supply chain portfolio that we are launching in preview. We had announced a partnership between FedEx and Microsoft, in January of 2022, to launch a cross-platform, logistics-as-a-service solution for brands. This partnership is now in preview. As e-commerce is exploding, businesses are challenged with growing their brand affinity while operating profitably to meet their consumer expectation like delivering orders in two days and offering a seamless returns experience. To achieve this, we are combining data insights from FedEx with order insights from Dynamics 365 Intelligent Order Management so that brands can optimize their transportation, and proactively overcome delays and disruptions enroute to deliver customer orders on time, in a cost-effective manner.
This partnership will also bring a powerful returns management experience to Dynamics 365, including hassle-free returns options at over 60,000 FedEx drop-off locations, convenient at-home pickups, printer-less QR return labels, and no-box returns. Ultimately, Microsoft and FedEx’s intelligence-driven logistics return services will empower brands with end-to-end visibility of customer returns while also allowing them to update consumers in real-time on the status of their return and refund generation.
Next, we are also excited to announce that we will launch embedded Microsoft Teams collaboration within Dynamics 365 Intelligent Order Management in preview on May 15, 2022.
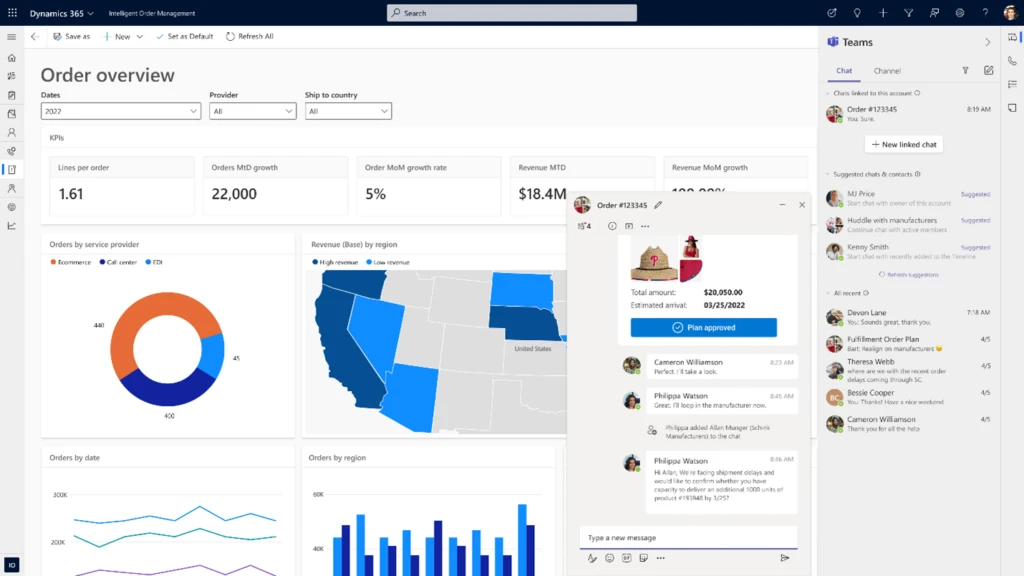
This enables hybrid supply chain teams to seamlessly connect over chat, share screens for discussion, post updates on issues in Teams. On top of improving communications, users will also be able to collaborate by sharing sales orders, return orders, and fulfillment order tracking data more effectively, all without exiting their flow of work within Dynamics 365 Intelligent Order Management. These capabilities help build a hyperconnected business that empowers people to collaborate as one business, everywhere—so people can thrive wherever, and however, they work.
Digital transformation of supply chains
We recommend three initiatives to kick start the digital transformation of your supply chains for a resilient and sustainable future—enhancing supply chain visibility, improving collaborative capabilities for better decision making, and designing sustainable operations with a circular economy in mind. You can achieve this by surrounding your existing supply chain and ERP systems without replacing them. Let us dive deeper into these areas and get a sneak peek into how some of our customers are transforming their supply chains.
Enhancing supply chain visibility
It is easier said than done to get real-time supply chain data across the value chain. At Microsoft, we have been investing in bringing new capabilities within our Dynamics 365 Supply Chain portfolio to market over the last year to really help organizations enhance visibility into every aspect of their value chain.
With the latest enhancements to Inventory Visibility Add-in, a highly scalable microservice for Dynamics 365 Supply Chain Management, companies can pull inventory from multiple third-party systems, allowing them to create a single, global view of all inventories. By creating one pool of global inventory from which all orders can pull, companies can often increase inventory accuracy and thereby maximize sales opportunities. Plus, when coupled with the soft reservation capability, sales order fulfillment can avoid over-selling, effectively mitigating the risk of missed sales opportunities that may challenge some organizations.
Coca-Cola Beverages Africa (CCBA) is the number one Coca-Cola bottler in Africa and the eighth largest globally by revenue.
“CCBA is currently implementing a set of Dynamics products including Dynamics 365 Supply Chain Management with Inventory Visibility, Field Service, and Customer Engagement products. CCBA envisage using Inventory Visibility to provide critical parts availability to field service technicians and to validate in near real-time the sales demands generated from Dynamics Customer Engagement. It will also be a key component of CCBA’s integrated Advance Warehouse Management solution. Eventually, all the orders and inventory journals will be synced or directly created in Dynamics 365 Supply Chain Management for financial and logistics processing.”—Elmar Els, Enterprise and Integration Architect, Coca-Cola Beverage Africa (CCBA).
Improve decision making with enhanced collaboration and a data-first approach
From a commissioned study conducted by Forrester Consulting on behalf of Microsoft in March 2022, we learned that over one-third of supply chain and operations leaders surveyed are taking steps to improve productivity through system and process improvements to mitigate future challenges.1 While it is imperative to generate insights from real-time supply chain data, the ability to act quickly on these insights is a whole different ball game. Organizations need to collaborate effectively across the different functions globally and with external suppliers and logistics partners to proactively overcome disruptions so that the orders can be delivered on time.
From the Forrester study, it’s clear that transformation is taking place across the entire customer journey, with nearly a third of businesses wanting to improve their operating model by making processes more streamlined across the board. To achieve their goals, companies require a tactical focus on being data-driven, improving the customer journey, and driving operational efficiency at scale.1
Peet’s Coffee is a California-based brand that delivers craft coffee and tea. They offer a variety of products—from a single cup to k-cups, capsules to whole beans—for sale in its stores, online, and in the supermarket.
Pre-2020, Peet’s Coffee ran the business on a dated and highly customized, on-premises system and Excel spreadsheets. The company had reached the point where the legacy system was near the end of its life and, after a rigorous software selection process, found Dynamics 365 to be the most comprehensive solution for a multi-channel organization with the best flexibility to adapt to the unique needs of coffee production.
“…Dynamics 365 gives us the cloud-based architecture we require to support the growth requirements of the business. The combination of Dynamics 365, Power Platform, and Azure cloud services provides Peet’s with a scalable and supportable technology foundation for the future.”—Allan Smith, Chief Information Officer, Peet’s Coffee.
By the early days of 2020, Peet’s Coffee had begun a digital transformation process by implementing Dynamics 365 Finance and Dynamics 365 Supply Chain Management. But what Peet’s Coffee couldn’t have planned for was the dramatic shift in demand that stay-at-home orders would create with the onset of the pandemic. Suddenly, Peet’s Coffee saw sales volume from its traditional channels, wholesale and coffee shops, plummet, while direct-to-consumer (DTC) and grocery channel sales surged 2x. Peet’s Coffee radically modified its implementation plan for Dynamics 365 to support immediate business needs. Ultimately, Peet’s Coffee adopted a new business model (DTC) and pivoted to supply grocery demand while successfully completing the implementation.
“…with the pandemic…it has been a heck of a year. I’m pleased with the investments we made. I’m pleased with the Blue Horseshoe relationship. I’m glad Dynamics 365 is live at Peet’s. But I wish we had done it earlier.”—Eric Lauterbach, President, Peet’s Coffee.
Reverse supply chains and circular economies
One way that manufacturing organizations are improving sustainability is by standing up circular economies. Circular economy, or circularity, is rooted in reverse supply chain management, which deals with what happens after a product’s useful life.
Setting up these circular economy flows can be challenging without an agile and composable supply chain management application. The Microsoft Circular Center program uses Dynamics 365 Supply Chain Management and Microsoft Power Platform to facilitate the reuse and recycling of servers and hardware within our datacenters, which is part of our commitment to achieving zero-waste and carbon-negative operations by 2030. To date, the Circular Centers model has achieved 83 percent reuse and 17 percent recycling of critical parts while contributing to the reduction of carbon emissions by 145,000 metric tons CO2 equivalent.
“We were looking for a warehouse management system that would allow us to model all the product flows that we needed while also connecting to datacenters and other systems used to manage our cloud assets. Dynamics 365 had all these functionalities to build exactly what we needed.”—Anand Narasimhan, General Manager of Cloud Supply Chain Sustainability, Microsoft.
Stay agile and resilient
In addition to the new integrations for Dynamics 365 Intelligent Order Management and the customer stories and new features covered here, we are also honored that Gartner® has recognized Microsoft as a Leader in the 2021 Gartner Magic Quadrant™ for Cloud ERP for Product-Centric Enterprises for Microsoft Dynamics 365. To learn more, please check out the Gartner Magic Quadrant and visit our Build a Resilient and Sustainable Supply Chain webinar.
Microsoft Dynamics 365 Supply Chain solutions enable organizations to create a digital supply chain that connects global teams, suppliers, and logistic partners for end-to-end visibility and frictionless collaboration. Our agile and composable Supply Chain solutions unify siloed data sources in real-time to detect opportunities, predict and overcome disruptions, and deliver sustainable competitive advantage. Reach out to learn more or get started with a free trial of Dynamics 365 Intelligent Order Management.
Sources:
1- A commissioned study conducted by Forrester Consulting on behalf of Microsoft. March 2022.
Gartner does not endorse any vendor, product or service depicted in its research publications and does not advise technology users to select only those vendors with the highest ratings or other designation. Gartner research publications consist of the opinions of Gartner’s Research & Advisory organization and should not be construed as statements of fact. Gartner disclaims all warranties, expressed or implied, with respect to this research, including any warranties of merchantability or fitness for a particular purpose.
GARTNER and MAGIC QUADRANT are trademarks and service marks of Gartner, Inc. and/or its affiliates and are used herein with permission. All rights reserved.