
3 practical ways industrial AI is reshaping manufacturing
Manufacturers are facing unprecedented demands to achieve greater efficiency. While not a new concept, transformation now depends on how organizations leverage the data generated from their manufacturing assets, processes, and people. Today, maturing Internet of Things (IoT), cloud, and AI solutions can enable every industry to scale innovation for greater insight and impact. Within manufacturing, AI plays a pivotal role in this change, connecting operational (OT), information (IT), and engineering (ET) technologies across the value chain, streamlining how products are designed and built, as well as optimized the long-term operation of factories and facilities.
At Microsoft, our mission has always been one of empowerment. AI furthers this mission. When harnessed together with modern compute and infrastructure, Microsoft AI offers unprecedented access to information that can help solve complex manufacturing problems faster. To showcase this innovation, we recently attended the International Manufacturing Technology Show (IMTS) 2024 in Chicago, Illinois, and demonstrated how Microsoft and its partners are accelerating industrial transformation outcomes with AI. Read on to experience IMTS for yourself, with our highlights and the 3 areas we believe the Microsoft Cloud for Manufacturing and AI are driving real industry impact.
- Design better products with AI-powered insights
- Build products smarter with AI-optimized manufacturing
- Modernize frontline operations with AI-assisted workers
Design better products with AI-powered insights
Design is the cornerstone of manufacturing, shaping not only product functionality, aesthetics, and performance but influencing production efficiency, material use, and long-term sustainability. This critical stage presents significant opportunities to optimize manufacturing processes and reduce costs that are often locked in early. With generative design and AI-enabled solutions like predictive modeling and digital twins, we can analyze real-time performance data and simulate alternatives rapidly to minimize material waste, reduce errors, and improve time-to-market.
Moreover, for many modern connected products, software is an increasingly significant component—driving functionality, value, and the transformation of traditional dynamics. Generative AI streamlines software development by accelerating code generation with tools like Github Copilot, allowing engineers to iterate faster, improve overall quality, and design more sustainably. The combined impact is a more agile, efficient development process that reduces time-to-market, enhances product performance, and fosters sustainable innovation. As software continues to integrate deeper into connected products, generative AI empowers engineers to push the boundaries of what’s possible within design and manufacturing.
Harnessing data for streamlined product development with PTC
In the Microsoft booth, our partner PTC demonstrated the impact AI can have on product lifecycle with a well-managed digital thread. Their demo showed how Vestas, a wind turbine manufacturer, leverages PTC’s design, Application Lifecycle Management (ALM), and Product Lifecycle Management (PLM) solutions to develop products. PTC’s new digital thread solution uses Azure and Microsoft AI to bring these tools together to enable real-time data synchronicity, traceability, and version control across Vestas’ product lifecycle. This single source of truth simplified the development process and enabled Vestas to continue reusing valuable data throughout the product’s lifecycle.
Build products smarter with AI-optimized manufacturing
Manufacturing success today requires a seamless integration of materials, technology, and resources. With these complex environments, AI is changing how we think about industrial operations. The merging of physical assets with AI, IoT, and automation solutions is enabling manufacturers to optimize production, reduce downtime, and improve real-time decision making for greater competitiveness.
accelerating transformation with Microsoft ai
Read the blogMicrosoft Cloud for Manufacturing centralizes data in the cloud, unifying its structure. Once organized, AI solutions can extract data’s hidden value analyzing it for insights, including predictive maintenance by identifying shop floor patterns and anomalies that may indicate potential equipment failures. AI-enabled factories allow manufacturers to better manage supply chains, anticipate these production shifts, and optimize their resource allocation.
For mission-critical operations, Azure IoT Operations ensures your data is processed on-premises for immediate action, before being sent to the cloud for further analysis. Azure IoT Operations takes an adaptive cloud approach, supported by Azure Arc, which enables manufacturers to unify data across their hybrid, multi-cloud, and edge environments. An adaptive cloud approach simplifies infrastructure management and security while maximizing resource utilization and ensuring AI-powered solutions scale across production lines and multiple sites. By adopting this approach, manufacturers can streamline operations, improve scalability, and establish a standardized architecture, ensuring resiliency and continuous improvement across the enterprise.
Enabling OT intelligence for autonomous operations with Rockwell
AI has already demonstrated its ability to digest information and offer accurate recommendations. How does this translate to manufacturing factories? Rockwell demonstrated how IoT solutions can enlighten older OT assets and processes. Rockwell enables organizations to transform their factory equipment into IoT-enabled assets. This live operational data is then centralized in the cloud through Azure IoT Operations, where predictive AI can automatically identify and address maintenance needs, enhance workflows, and perform tasks that once needed onsite staff.
Modernize frontline operations with AI-assisted workers
Frontline workers and service teams are the backbone of manufacturing operations. Their expertise, adaptability, and problem-solving skills are critical for maintaining production efficiency—ensuring quality control and driving continuous improvement in environments where the digital world meets the physical world. When empowered by AI, these workers become decision-makers freed from repetitive tasks. AI allows frontline workers from the factory floor to the field to focus on higher-value activities, improves their productivity, and enables them to adapt to the evolving demands of modern manufacturing.
Generative AI enables service teams to seamlessly create work orders from unstructured data like emails, efficiently schedule resources, and provide timely support—particularly during high-demand periods. For frontline workers, AI offers fast and intuitive access to essential information, eliminating the need to manually sift through long standard operating procedures, equipment manuals or contact expert support. By delivering the right information at the right moment with natural language prompting, generative AI not only improves first-time fix rates but also accelerates worker upskilling, preparing them for more complex responsibilities and driving long-term productivity gains.
Delivering exceptional customer service with Dynamics 365 Field Service
At IMTS 2024 we showcased how Microsoft Copilot in Dynamics 365 Field Service is enabling workers to solve problems more efficiently and deliver exceptional customer experiences. Delivering exceptional service is key for building customer preference and loyalty. Copilot in Dynamics 365 Field Service can help service managers and technicians efficiently create workorders, schedule workers and find the information they need to resolve issues right the first time while keeping customers updated at every step of the process. With the added capabilities of Microsoft Dynamics 365 Remote Assist capabilities in Microsoft Teams, frontline workers can call for expert help and utilize augmented reality features such as spatial annotations reducing asset downtimes and efficient service experience for customers.
Continuing AI conversations beyond IMTS 2024
Manufacturing is undergoing a profound transformation. It is clear, AI will be at the heart of this change. From revolutionizing product design with AI-driven insights and optimizing manufacturing processes with predictive analytics to empowering frontline workers with easy access to information, AI is fundamentally reshaping how industries operate. IMTS 2024 underscored our vision for manufacturing and the impact AI will have on industrial operations. From PTC to Rockwell to Microsoft Copilot in Dynamics 365 Field Service, AI is driving innovation and enabling manufacturers to overcome operational bottlenecks.
As AI adoption accelerates, organizations will face challenges such as inadequate data, expertise gaps, and governance. Microsoft is committed to helping manufacturers overcome these obstacles and realize the full potential of AI. By combining modern cloud infrastructure and compute with powerful AI tools, Microsoft can enable every organization to scale their AI initiatives across multiple sites and functions, moving them beyond “pilot purgatory” to achieve long-term, sustainable transformation.
Explore Microsoft solutions
Now is the time. Along with its partners, Microsoft can help every manufacturer unlock the value in their data, streamline operations, and drive greater value chain efficiency. Whether you’re just beginning your journey or looking to scale, Microsoft can support you at every stage.
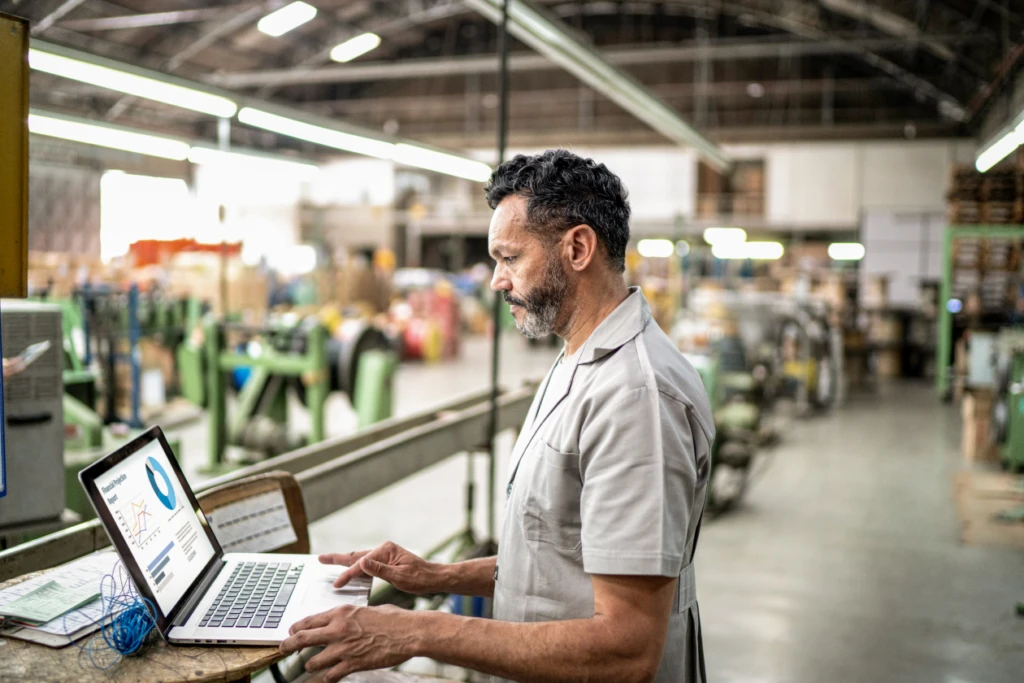
Industrial transformation
Accelerate how your organization designs, builds, and operates with AI
- Learn how Microsoft can help you overcome barriers to AI adoption and drive real impact in your manufacturing value chain by reading this report we created in collaboration with MIT Technology Review Insights.
- Explore how Microsoft is helping other organizations accelerate their transformation on our industrial transformation webpage.